Recruiting Information
Recruiting Information
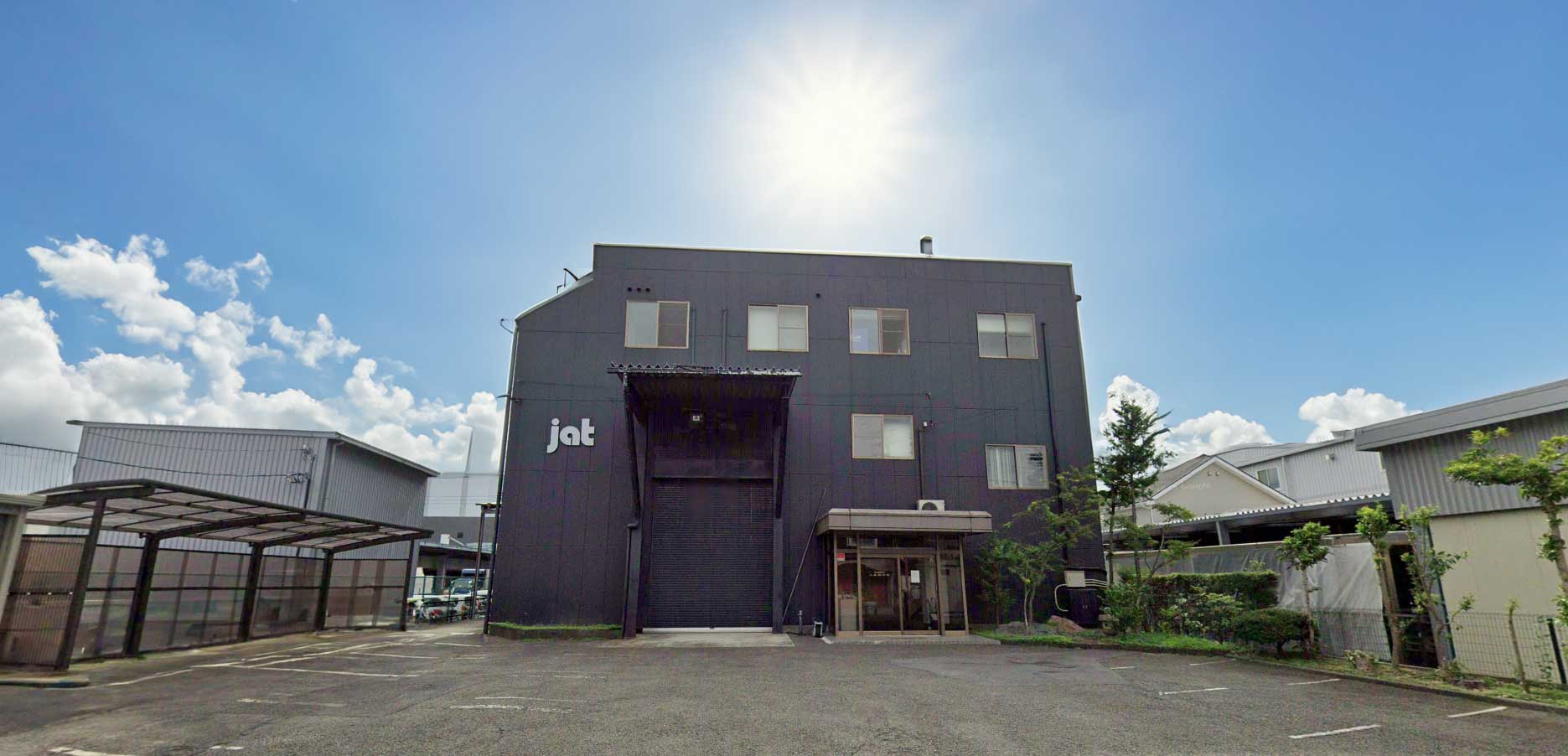
Quality Assurance Department
Mr. S.H. Joined the company in 2022
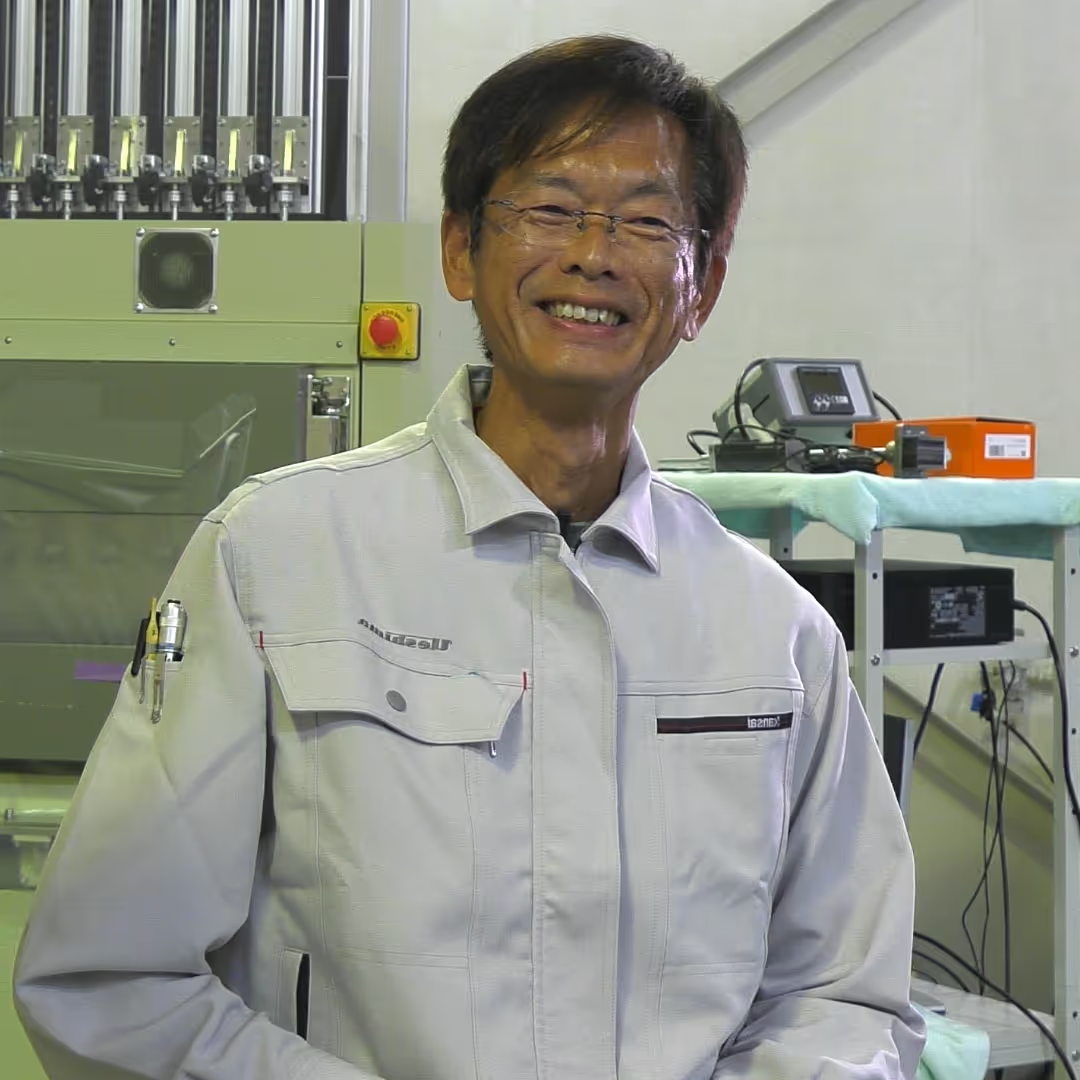
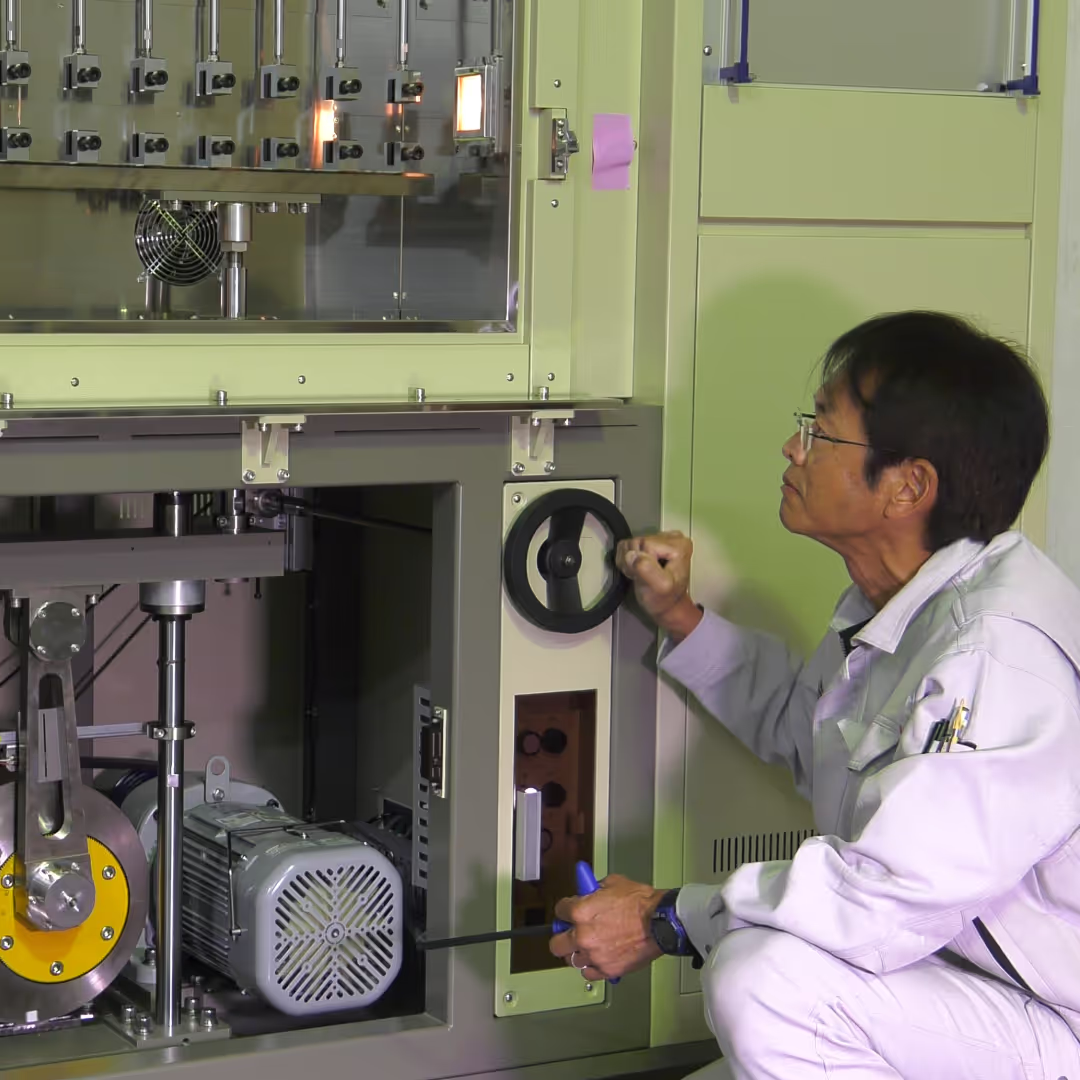
Rewarding at UESHIMA
Our products are mainly used by major manufacturers for research and quality inspection of materials that are essential to everyday life.
There are also many products that have been used for many years, and I feel very rewarding when I visit the site and handle repairs due to problems that occur because of that, and receive words of appreciation from users.
Why I chose UESHIMA
In my previous job, I was doing shipment inspections and field service for foreign-owned measuring instruments. The turnover of employees was drastic and my mental and physical condition was often disrupted, but at our company, I felt that I could work healthily for a long time, taking into consideration holidays, overtime, business trips, etc., so I applied. Also, being able to make use of my experience and skills up until now was a plus.
Workplace atmosphere
Basically, I'm left to autonomy, so being able to schedule my own makes it easier to work.
When projects overlap and the response is tough, you can rest assured that you can follow up as a department.
Even when it is technically difficult to respond, there is a cooperative system in place with other departments, so there is no need to worry alone.
Future goals
I would like to try to make the products you continue to use evolve for the better and become products that are even easier to use and make you happy. Also, new products have been developed in response to changes in the times, and I would like to be involved in those products and gradually build up my strength so that I can contribute to society.
Regarding quality management personnel
Quality control work is basic to reliably perform each inspection so that each product can be used with peace of mind, but it is also important to give feedback if there are any improvements so that they can look at it from the user's point of view and use it more satisfactorily.
For on-site calibration, it is better if maintenance and parts replacement suggestions can also be made according to actual usage conditions.
Typical daily schedule
8:15 Departure from the company
9:30 User visits company and admission procedures
10:00 Check the actual machine status and start calibration
12:00 lunch
12:50 Work resumed
15:00 Finish work, create service report, report results
17:15 Return to work, clean up
17:30 Leave the office
Contact
We're here to help. For more information about our products and services, please fill out the form on the right.
Contact
For orders for repairs, calibrations, and services, please contact us using the contact details listed below.